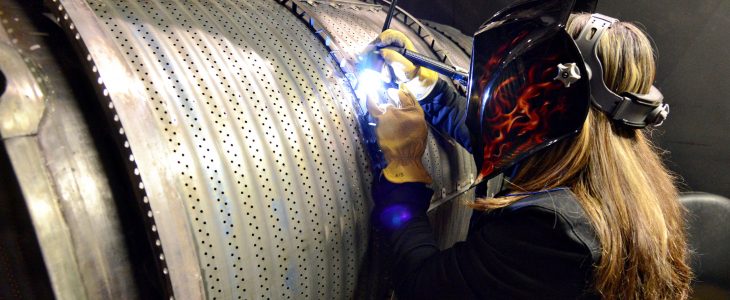
Inspecting damages on a pipeline can be a costly business. The pipeline can be in the inaccessible area, freezing or sizzling climate, underground. Examining Corrosion from outside and inside, impact damage or service related fracture is taken in concern to do the NDT in a particular pipeline system. Ultrasonic Testing is one of the most widely used NDT technique in petrochemical industries. A specially customized Long Range ultrasonic system is equipped in each doubtfull section of a pipe to find the Corrosion, erosion, mechanical damage, and fatigue cracking. Its purpose is to provide a rapid means of screening in pipes and pipelines to extend their life span up to its maximum.
Flaw Detector
It’s a programmable 24 channel unit which allows us to implement some current procedure upgrades and allows expansion for the future. For this, we have an AC/DC supply, lithium-ion battery pack, low-frequency ultrasonic System. The system essentially consists of two parts, one is mounted on the pipe/pipeline which is to be inspected and the other is PC with electronic Switch mounted in vehicle or cabin after 50m away, so as to control the test from a remote area.
RT Flaw Detector
Not with standing its high affectability, the strategy for the radioisotope test has exceptionally restricted uses since the time has come devouring, hard to work, little in identification scale, hazardous to the operator. Also, when several bends are organized in parallel, flaw detection can’t be done
UT Flaw Detector
In view of the point-to-point contact between the traditional detector and the testing specimen, it is somewhat hard for the detector to direct ultrasonic wave into the pipe twists due to the unregular curved surface of the external circular segment at a pipe bend. To accomplish proper contact, the indicator needs a concave surface through grinding. In any case, such a grinding procedure will change the various pre-set parameters of the detector. Also, the thickness of the ground wedge of the ultrasonic detector will be incredibly decreased and the activity life of the detector will be considerably abbreviated. Additionally, the commotion level on the monitor will be Increased and the precision of defect recognition will be influenced
Radiography in pipeline testing
Radiographic testing utilizes ionizing radiation to achieve an image of a pipeline Section on several viewing angles. This can be carried out using x-ray or gamma rays. Initially, the film is mounted on the pipe section and set up the x-ray tube carefully. The setup is placed in an isolated area will all operations carried out remotely to avoid coming in contact with the exposed radiation. The examiner adjusts the voltage, current & Duration depending on the investigated material and the wall thickness of the pipeline. Soon after the initialization the x-ray beam will penetrate through the given pipe section and generate a radiographic image on the film or imaging plate. An experienced inspector will interpret the obtained image and determine the quality of the image and identify whether the quality meets the standard.