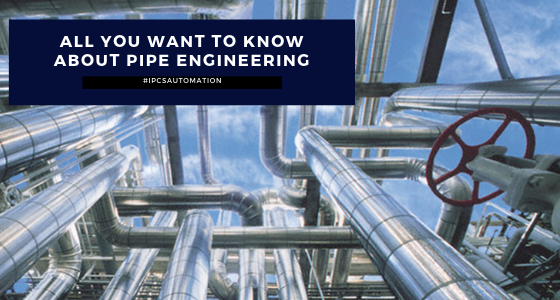
Piping
Piping is incredibly vital for each process plants. Product flow and outflow are applied through the pipes. If we glance at the oil exploration, refineries and organic compound treatment platform one factor that catches the eye is that the sophisticated fascinating network structure of piping. The purpose of this sophisticated piping structure is to move varied process materials like fluid or gases from one place to a different. Process plant could be a place where a series of activities performed particularly in order to convert refined stuff into a useful product.
Piping system
A piping system could be a network of pipes, fittings and valves meant to perform a selected job i.e. to hold or transfer fluid from one instrumentality to a different. Some of the other rigorous examples included in the piping systems are steam piping in a power plant, piping in a dairy farm for the flow of milk. Piping in a paint manufacturing company, oil piping in a refinery and so on
Components of the piping system
The main components of a piping system are pipes, fittings, and valves.
Pipes: A pipe could be a straight pressure tight hollow cylinder, utilized in the pipe system to move liquid, gas and generally solid.
Pipe Fittings: pipe fittings are generally used to join/connect the pipes to construct an extended pipe system. The commonly used fittings are flanges, elbows, tees, reducers, expansion bellows, etc.
Valves: valves are customized to stop, divert and control the fluid flow. Some of the common valve types that are taken based on the intended function and the applications are gate valves, globe valves, ball valves, control valves, butterfly valves, etc.
Along with these all components, some additional components like strainers, traps, expansion loop, etc. used to keep the fluid clean and accommodate expansion/contraction due to temperature variation.
Regular Pipe Checking
Steel pipes will have a protracted time if they are well monitored and repaired when broken. In large power plants like oil refineries will have to face large disasters in the absence of periodic inspection.
What should manufacturers consider when inspecting a pipe?
The technical manufacturers should always keep the record of both offline inspection taken during maintenance and online monitoring. If the pipes show any trace of chemical corrosion, the carbon steel component must be immediately replaced with more corrosion resistant material. In the insulated steel pipe, the possibility of corrosion will be more i.e. Corrosion under insulation is quite common in the pipes. We have found that about 10% of all maintenance cost can be caused by Corrosion under insulation.