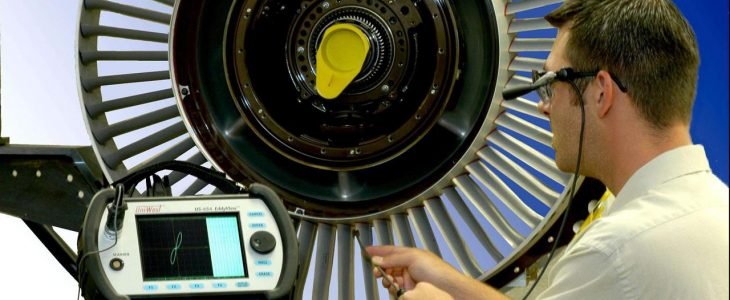
Regardless of the dread that emerges from hearing updates on a plane accident, flying is as yet one of the most secure methods of movement for some reasons, not the least of which incorporates flying machine/aircraft maintenance.
NDT and Aircraft Maintenance
Consistently scheduled maintenance is an integral part of guaranteeing the aircraft safety.
A wide scope of NDT methodology guarantee that not a solitary fabricated segment achieves service without first finishing a progression of stringent tests.
Actually, today, NDT is trusted as an assurance for security in the aviation field,” Aeroplane endures numerous sorts of basic crumbling including erosion, corrosion, fatigue, imperfections, fabrication defects, operation and maintenance, and unforeseen loading. In aeroplane support, it is basic to assess surfaces for any harm that may exist so as to decide the degree of fix work required, regardless of whether that happens as the consequence of manufacturing or while the aircraft is in service. During scheduled maintenance, non-destructive testing (NDT) is one of the fastest, most affordable approaches to perform assessments, and the best way to find a defect that is not noticeable to the unaided eye. NDT is utilized to discover flaws on and under the surface, just as to identify leaks, decide the area of basic structural insufficiencies, and decide dimensional measurements
Visual Testing inspection in Aircraft
Visual reviews are the most established and least complex strategy for non-dangerous testing. It’s frequently said the human eye is the most dominant NDT device. Visual investigations of aircraft structures and parts for harm, for example, cracks, corrosion and misalignment will regularly be the primary indication of an issue.
Different types of equipment are utilized for visual investigations, from magnifying glasses and mirrors to video borescopes for review hard to achieve places, charge-coupled device and remote survey systems.
UT inspection in Aircraft
UT has many uses in the aerospace industry including detection of:
- Surface and subsurface defects
- Main structural fittings of landing gear legs
- engine attachments
- Aircraft structure joints and pylons
- Bolts located in critical areas
- Adhesive bond quality of lap joints and composite structure;
- Thickness measurement after damage or corrosion removal.
LPT inspection in Aircraft
Liquid penetrant testing is another simple and speedy strategy broadly utilized in the aerospace industry to recognize surface deformities and basic harm in non-porous materials.
Radiography in aerospace
Radiography in aerospace can utilize both x- Ray beams for thin materials and gamma beams for thicker materials. Generally film has been utilized to capture the picture yet is being supplanted by computerized strategies. A further ongoing development is 3D Computer Tomography (CT) checking, which capture multiple x- Ray beams of a test article to develop a cross-area perspective on the specimen on a computer monitor.