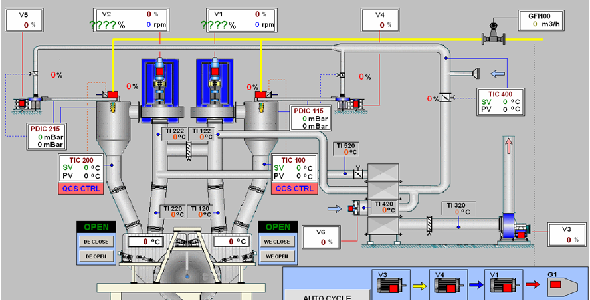
A distributed control system (DCS) is a platform for automated control and operation of a plant or industrial process. A DCS combines the following into a single automated system: human-machine interface (HMI), logic solvers, historian, common database, alarm management, and a common engineering suite. Over 10,000 plants entrust DCS to deliver their production goals
It differs from the centralized control system wherein a single controller at central location handles the control function, but in DCS each processing element or machine or group of machines is controlled by a dedicated controller. DCS consists of a large number of local controllers in various sections of plant control area and is connected via a high-speed communication network.
In DCS control system, data acquisition and control functions are carried through a number of DCS controllers which are microprocessor-based units distributed functionally and geographically over the plant and are situated near the area where control or data gathering functions being performed as shown in the figure above. These controllers able to communicate among themselves and also with other controllers like supervisory terminals, operator terminals, historians, etc.
DCS is most suited for large-scale processing or manufacturing plants wherein a large number of continuous control loops are to be monitored and controlled. The main advantage of dividing control tasks for distributed controllers is that if any part of DCS fails, the plant can continue to operate irrespective of the failed section.
These attributes of DCS can be observed in its architecture shown in the diagram. The basic elements comprised of a DCS include engineering workstation, operating station or HMI, process control unit or local control unit, smart devices, and communication system.
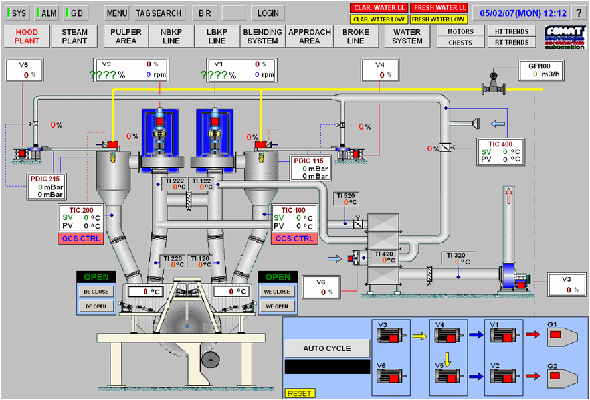
