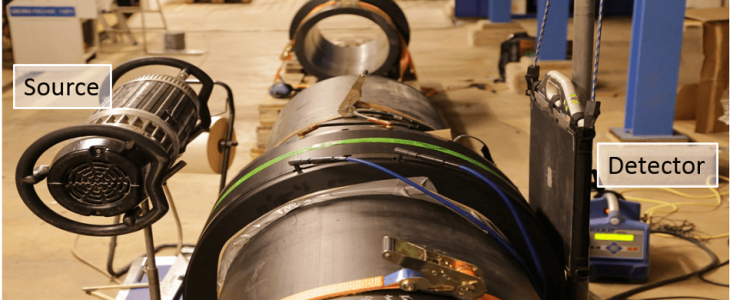
Radiographic testing is generally utilized in industry segments including aerospace, power generation, construction, petroleum, chemical and automotive, and for all types of components and parts. The system is generally utilized on welded parts, castings, forgings, composites and is additionally utilized for finding corrosion identification and measuring of wall thickness. During a radiographic procedure, an x-ray beam is passed through the body. A part of the x-ray beams are retained or dispersed by the interior structure and the rest of the x-ray beam design is transmitted to a detector/identifier with the goal that a picture might be recorded for later assessment. The recording of the example may happen on film or through electronic methods.
Interpretation of radiographs happens in three fundamental steps:
Detection
Interpretation, and
Evaluation
These means utilize the radiographer’s visual sharpness. The capacity of a person to identify discontinuities in radiography is additionally influenced by the lighting condition in the spot of the survey, and the experience level for perceiving different highlights in the image.
General Welding Discontinuities
- Cold lap
- Porosity & Cluster porosity
- Slag inclusions
- Incomplete penetration (IP) or lack of penetration (LOP)
- Internal concavity or suck back
- Internal/root undercut and External/crown undercut
- Offset or mismatch
- Inadequate & Excess weld reinforcement
- Cracks
- Tungsten & Oxide inclusions
- Burn-Through
The significant goal of radiographic testing of castings is the revelation of imperfections that unfavourably influence the quality of the product.
Modern radiography is a strategy for non-destructive testing where numerous parts can be inspected to confirm the inside structure and integrity of the product. Modern Radiography can be performed using either X-Rays or Gamma Rays. Both are types of electromagnetic radiation. The difference between the types of electromagnetic radiations is identified with the wavelength. X and gamma rays have the shortest wavelength and this property prompts the capacity to penetrate, and exit different materials, for example, carbon steel and different metals.
Radiographic testing can give a permanent film record of weld quality that is generally simple to interpret by an expert. This testing strategy is typically fit to approaching the two sides of the welded joint (except double wall signal image techniques used on some pipework). Despite the fact that this is a slow and costly method of nondestructive testing, it is a positive technique for detecting porosity, inclusions, cracks, and voids in the interior of welds. It is basic that certified faculty lead radiographic interpretation since the false interpretation of radiographs can be costly and affect productivity. Proper care should be taken radiographic testing. X-rays and gamma radiation are undetectable to the unaided eye and can have genuine health and security suggestions.