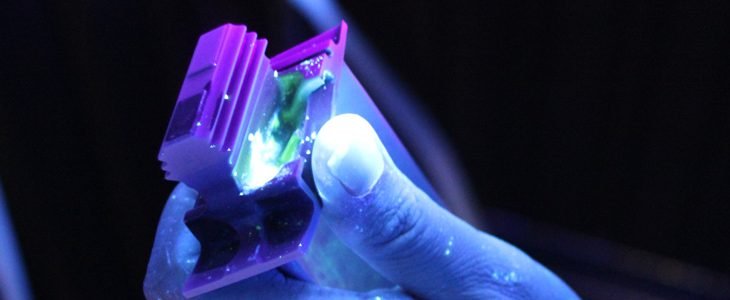
Non-destructive testing (NDT) is the way toward reviewing, testing, or assessing materials, segments or gatherings for discontinuities, or contrasts in attributes without disturbing the functionality/serviceability of the part or system. Other than NDT, there are different tests that are destructive in nature and are in this way done on a predetermined number of tests, rather than on the materials, segments or assemblies really being put into service.
These destructive tests are regularly used to decide the physical properties of materials, for example, resistance, yield fatigue toughness, fatigue strength, ductility, ultimate tensile strength, however, discontinuities and contrasts in material attributes are all the more adequately found by NDT.
Today nondestructive tests are utilized in assembling, manufacturing, fabrication and in-service inspections to ensure product integrity and reliability, to control fabricating forms, lower generation costs and to keep up a uniform quality dimension. During development, NDT is utilized to guarantee the nature of materials and joining processes at the fabrication stages, and in-service NDT assessments are utilized to guarantee that the items being used keep on having the integrity and the safety for the public
Defects monitored by NDT
Liquid Penetrant Testing
Used to find cracks, porosity, and different deformities that break the outside of a material and have enough volume to trap and hold the penetrant material. Fluid penetrant testing is utilized to assess enormous regions in all respects effectively and will take a shot at most non-porous materials.
Magnetic Particle Inspection
Used to review ferromagnetic materials that can be magnetized to find the defect by the cause of magnetic permeability effect in a material. Magnetic particle inspection can distinguish surface and close surface deformities.
Ultrasonic Testing
Used to find surface and subsurface deformities in numerous materials including metals, plastics, and wood. An ultrasonic review is additionally used to gauge the thickness of materials and generally characteristic properties of material dependent on sound speed and constriction estimations.
Radiographic Testing
Used to review practically any material for surface and subsurface imperfections. X-Rays and gamma rays can likewise be utilized to finds and measures internal features, hidden parts, hidden discontinuities, and to gauge thickness of materials.
Ultrasonic testing (UT) technique enables us both defects detecting and size measuring. But measurement using UT are difficult to assess because of many factors such as characteristics of the transducer, the transducer bandwidth, and center frequency, angle of inclination, depth and orientation of the defects, etc. Today without a doubt, extremely experienced administrators can perform a full assessment of the outcomes, particularly for coarse-grained materials (treated steel). In this manner, an extensive interest has been watched for devices that can help the operator in such tasks.