
A current to the pressure converter (I/P) converts an analog signal (4 to 20 mA) to a proportional linear pneumatic output (3 to 15 psig). Its purpose is to translate the analog output from a control system into a precise, repeatable pressure value to control pneumatic actuators/operators, pneumatic valves, dampers, vanes, etc.
The heart of the system is the flapper nozzle amplifier. It converts very small displacement signal (in order of microns) to the variation of air pressure. The basic construction of a flapper nozzle amplifier Constant air pressure (20psi) is supplied to one end of the pipeline. There is an orifice at this end. At the other end of the pipe, there is a nozzle and a flapper. The gap between the nozzle and the flapper is set by the input signal. As the flapper moves closer to the nozzle, there will be less airflow through the nozzle and the air pressure inside the pipe will increase. On the other hand, if the flapper moves further away from the nozzle, the air pressure decreases. At the extreme, if the nozzle is open (flapper is far off), the output pressure will be equal to the atmospheric pressure. If the nozzle is blocked, the output pressure will be equal to the supply pressure.
the controller used in process control is normally electronic and for actuation, a pneumatic actuator is the preferred. Thus there is a need for converting the electrical signal (often 4-20 mA) from the controller to pneumatic 3-15 psi signal. Such a scheme. It is similar to flapper nozzle, except there are an electromagnet and a permanent magnet on the left of the link. The current flowing through the electromagnet causes a force of repulsion between the electromagnet and the permanent magnet. An increase in current through the coil increases the repulsive force, thereby moving the link upward on the left-hand side and decreasing the gap between the flapper and the nozzle. The feedback action causes the increase in the output pressure and brings back the link in its equilibrium position.
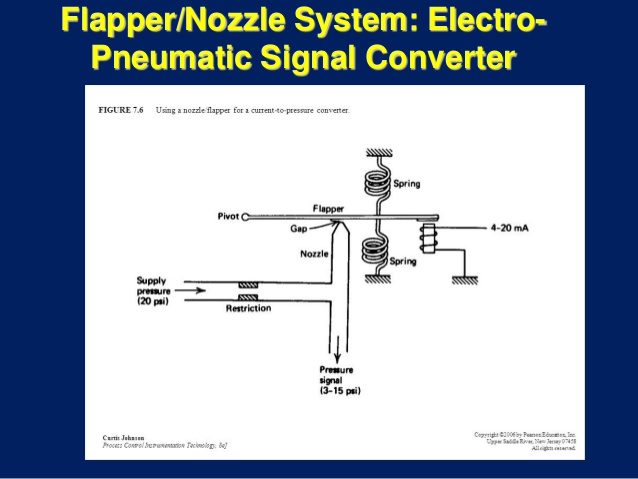
